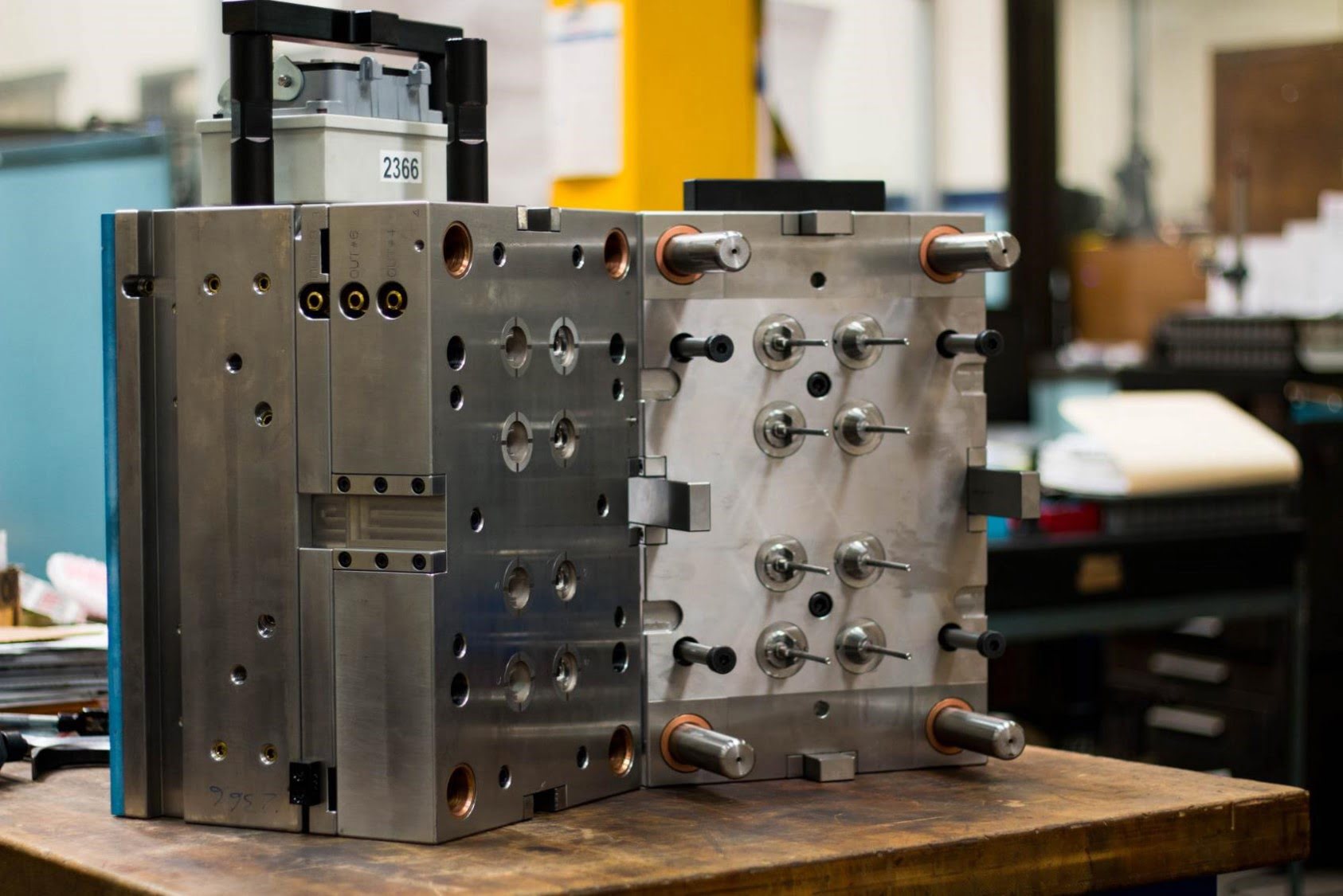
The plastic injection process involves injecting melted plastic into a mold to form a part. It is a fast and cost-effective way to manufacture many different types of products.
Injection molding can produce several types of defects. These include sprue marks, ejector pin marks and gate marks. These marks are the result of a poor tool design, injection speed or runner temperature.
Thermoplastics
Thermoplastics are a type of plastic that softens when heated and solidifies when cooled. They are commonly used in injection molding as a substitute for metals. They are also able to be re-melted and molded after cooling, making them ideal for high-volume manufacturing.
The injection molding process melts, injects and sets plastic into a mold fitted into a specialized hydraulic or electric machine. This technique is used to produce a wide range of products and components. Thermoplastics can be molded into complex shapes and are ideal for rapid production, as well as prototyping. They also have the advantage of being more flexible than thermosets, and can adapt to design changes. They can also withstand higher temperatures and are resistant to moisture and bacterial growth.
Thermosettings
Engineered thermoplastics are a special class of raw materials that are used in injection molding. They have high mechanical strength and resistance to heat, flame, water, chemicals, and abrasion. These types of plastics are ideal for use in the medical sector because they can withstand repeated tests and can be molded into a variety of shapes and sizes.
Unlike thermoplastics, thermosets become hard when heated. During the injection process, two fluid components are injected into a thermally isolated hot mould and chemically cross-linked. Then, valves close to isolate the injection system and the chemical precursors. This minimises the amount of time that the liquid thermoset spends in the injection barrel and screw, which improves cycle times. This is particularly important for high-volume programs, where every machine second counts.
Low-density polyethylene
LDPE is a type of polyethylene that is often used in plastic injection molding. It is a flexible and translucent material that offers great chemical resistance. It also has excellent moisture resistance. In addition, LDPE can withstand high temperatures for short periods of time.
Unlike HDPE, LDPE has less branching on its molecular chains, which allows it to be more flexible and stretchable. It also has better resistance to alcohols, dilute alkalis, and acids. It has poor resistance to mineral oils and oxidizing agents, however.
LDPE is manufactured by copolymerization of ethylene with an alpha-olefin co-monomer. The most common co-monomers are butene, hexene, and octene. This process is done using free radical polymerization with peroxides as initiators. Unlike other types of polyethylene, LDPE does not retain memory when strained.
High-density polyethylene
Polyethylene (PE) is the world’s most widely used thermoplastic material. It is lightweight and offers chemical resistance, durability, and electrical insulating properties. Injection molding companies use PE in a wide range of consumer, commercial and industrial applications. PE is made up of a family of polymers that vary by their crystallinity and densities, which in turn affect the stiffness and flexibility of the plastic.
PE injection molding uses the linear version of the polymer known as HDPE, which has a low degree of crystalline branches and is opaque. The more branched versions of this polymer, such as LDPE and LLDPE, are transparent and less rigid than HDPE. They also cannot tolerate the higher temperatures that HDPE can. Regardless of their differences, all PE grades exhibit good strength, impact resistance and malleability.
Polypropylene
Polypropylene is a versatile plastic resin that can be used for a wide range of applications. Its versatility is especially useful for making caps for consumer products. It is also commonly used in piping, such as for household and industrial use. Its strength and moisture resistance are two of its most important properties.
It has great fatigue resistance and can withstand a broad range of chemical reactions, making it ideal for automotive applications. Its superior moldability and resistance to bending makes it an excellent choice for fender lines, instrumental panels, door trims and battery cases.
It is also resistant to bacterial growth and sterilization, making it a popular choice for medical equipment. However, its exposure to high temperatures can release irritating vapors into the respiratory system.